
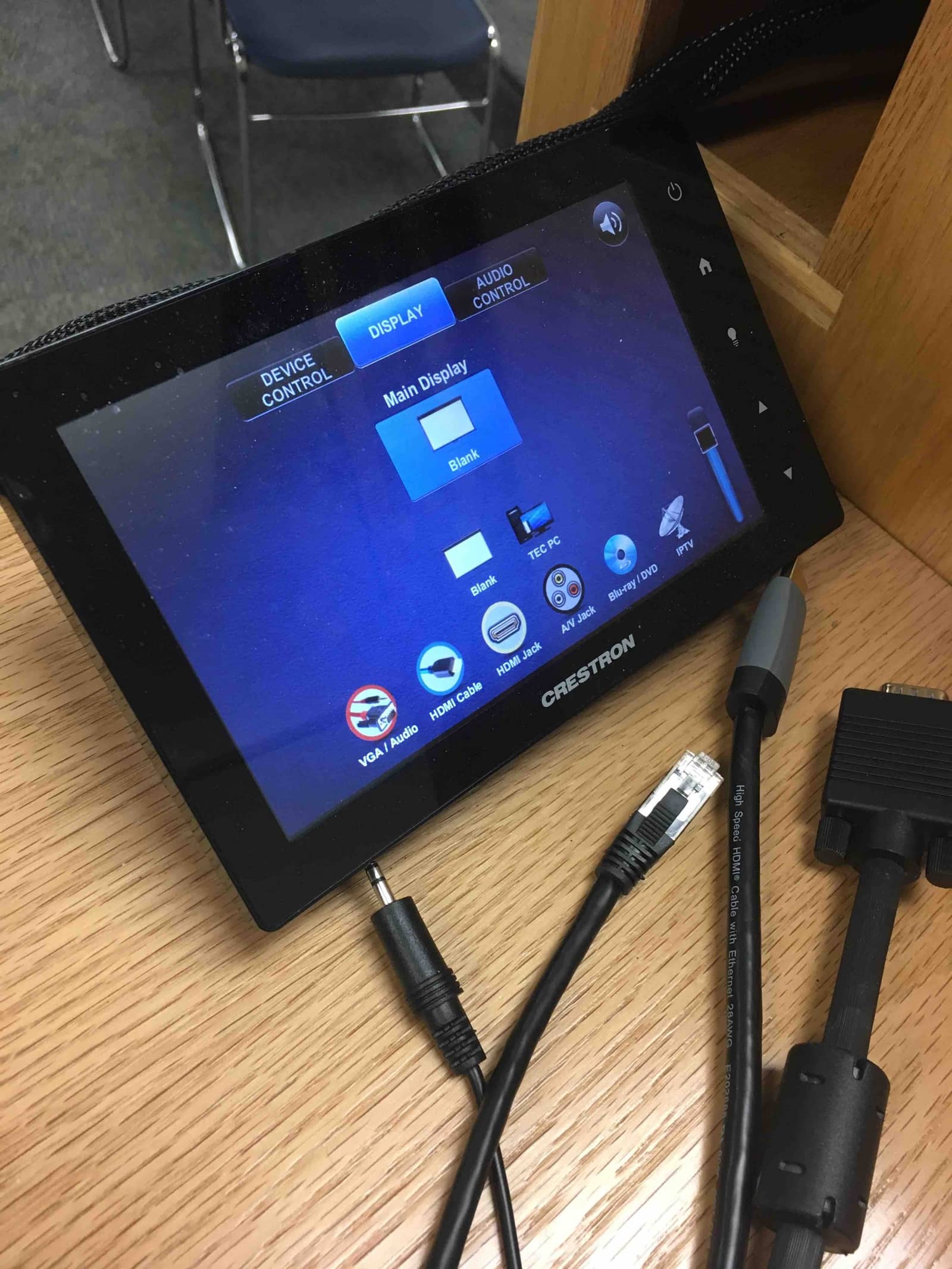
The steels were forged again to final density. The powders were placed in a mild steel can and forged in a stream of hydrogen gas at 1473 K. ODS Fe-18%Cr-2%W-0.2%Ti steels with 0, 0.35, 0.5, 1 and 1.5% Y (all compositions in weight%) dispersion were fabricated by mechanical alloying of elemental powders. Oxide dispersion strengthened (ODS) steels are being developed for future nuclear reactors. [Mechanical Metallurgy Group, IGCAR, Kalpakkam, Tamilnadu 603102 (India) [Department of Metallurgical and Materials Engineering, I.I.T-Roorkee, Uttarakhand 247667 (India) Laha, K. Kumar, Deepak [Department of Metallurgical and Materials Engineering, I.I.T-Roorkee, Uttarakhand 247667 (India) Prakash, Ujjwal, E-mail: [Department of Metallurgical and Materials Engineering, I.I.T-Roorkee, Uttarakhand 247667 (India) Dabhade, Vikram V. High yttria ferritic ODS steels through powder forgingĮnergy Technology Data Exchange (ETDEWEB) In addition, ductility and impact properties of P/M forgings with near theoretical density (99.5+ percent) were comparable to bar stock forgings The response of P/M forgings to heat treatment was comparable to that for wrought materials, and the resultant tensile and yield strengths were equivalent to the strength values described for wrought 4640 steel in AMS specification 6317B. At forging conditions which resulted in forgings with acceptable mechanical properties, complete die fill was accomplished at a forging ratio of 0.95, whereas incomplete die fill resulted at a forging ratio of 0.75. Forgings with densities from 99 to 99.8 percent of theoretical density were attained with a forging pressure of 20 to 40 tsi and preform temperatures of 2000 0 F and above. Die wall lubrication was comparable to admixed lubrication, and it simplified powder mixing and preform sintering operations. High density compacts required higher sintering temperatures due to the restricted mobility of the reducing gases in the pores. Relationships between interconnected porosity and total porosity for the various preform densities were determined. Variables studied were preform density, method of lubrication, preform sintering (time, temperature and atmosphere), forging pressure (20 and 40 tsi) and temperature (1850 0 F, 2000 0 F and 2200 0 F), and forging ratio (0.75 and 0.95). Prealloyed 4600 steel powder blended with graphite to yield 4640 was compacted into preforms and hot forged in a warm, closed die. The effects of processing variables on the mechanical properties of heat-treated powder metallurgy (P/M) steel forgings were determined. International Nuclear Information System (INIS) Properties of powder metallurgy steel forgings
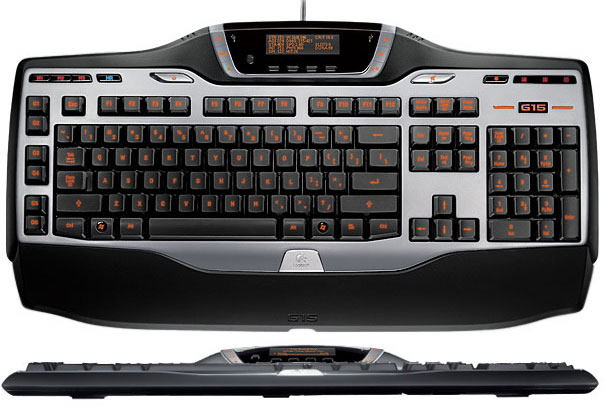
We must reach correct temperature in the furnace for raw steel to melt with less scalings. The correct choice of furnaces is also very important.
#PREFORM AV ENABLER FREE#
Free forging can be divided to hand forging and machine forging. We can separate steel forming to free forging and drop forging. The following work presents processes of steel forming, challenges when forging steel, forming machines suitable for forging and which choice of machine is most suitable for forging.
